Research Progress
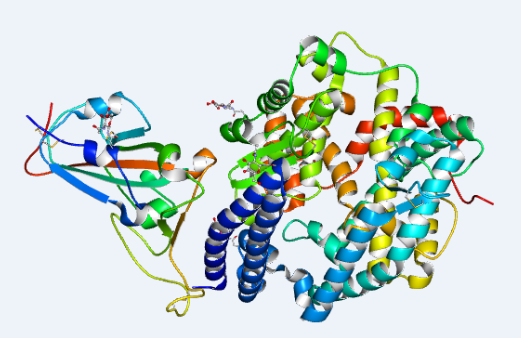
SSRF Helps on the COVID-19 Structure Determination to Understand the Infection Mechanism and Drugs R&D
To meet the urgent needs of determining the protein structure, Shanghai Synchrotron Radiation Facility (SSRF) has opened a green channel to fully support the research teams carrying out studies related to COVID-19. At the end of January, SSRF promptly rebooted the accelerator that was shut down for maintenance. Three protein crystallography beamlines reopened: BL17U1, BL18U1 and BL19U1, which also played a significant role in the studies of the previous epidemic like H1N1, H7N9, MERS, Zika, and Ebola.
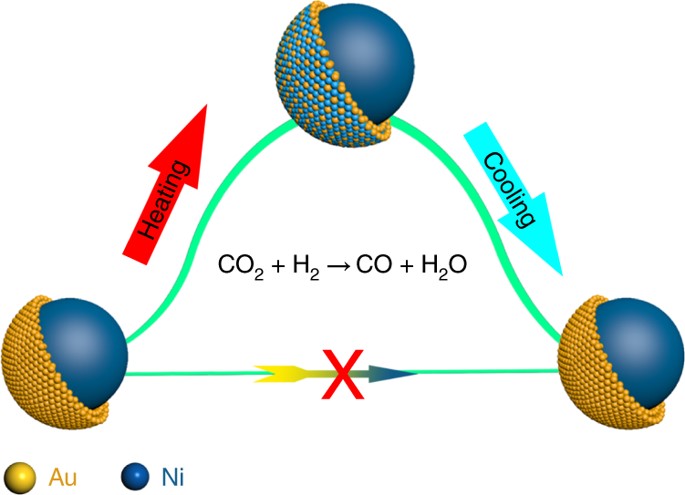
Researchers Reveal a Dynamic Mechanism for Ni–Au Bimetallic Nanoparticles during CO2 Hydrogenation
The high catalytic performance of core–shell nanoparticles (NP) is usually attributed to the syngergy of distinct geometric and electronic structures. Although the general assumption is that core–shell NPs maintain their configuration under working conditions, it remains unclear whether they maintain their structure throughout a reaction.Scientists recently reported a different working mechanism and demonstrated that the core–shell structure may not exist under a specific set of conditions, which overturns the conventional understanding.
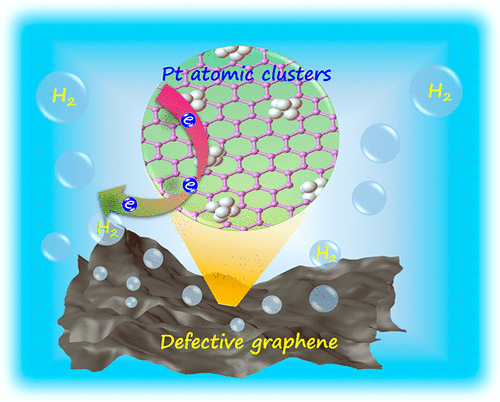
Novel Approach to Pt Electroless Deposition for Highly Efficient Hydrogen Evolution
The small size and large specific surface area intrinsically associated with Pt atomic clusters pose challenges in the synthesis and stabilization of Pt-ACs without agglomeration. A research team reported a novel one-step carbon-defect-driven electroless deposition (ELD) method to produce ultrasmall but well-defined and stable Pt-ACs supported by defective graphene (Pt-AC/DG) structures.
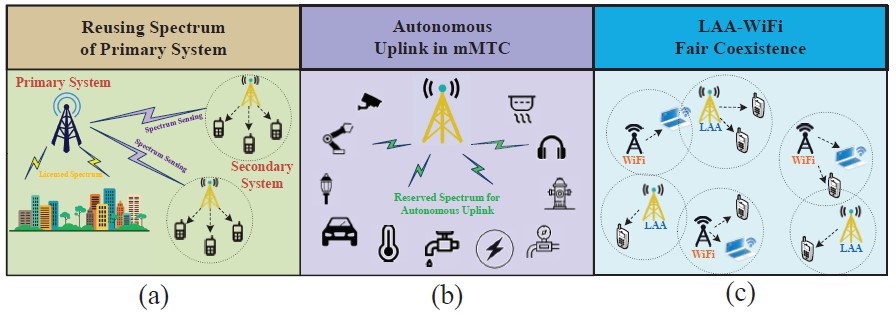
Researchers Develop an Intelligent Spectrum Sensing Technique for 5G communications
The ongoing 5G communication involves diversified scenarios with different characteristics and diverse requirements, which makes spectrum sensing methods difficult to serve various applications flexibly while maintaining satisfactory performance. Motivated by such a challenge,researchers provided a novel spectrum sensing technique, seeking a feasible way to combine the reinforcement learning concept with advanced spectrum sensing methods so as to optimize the performance of the cognitive radio network under multifarious scenarios in 5G communications.
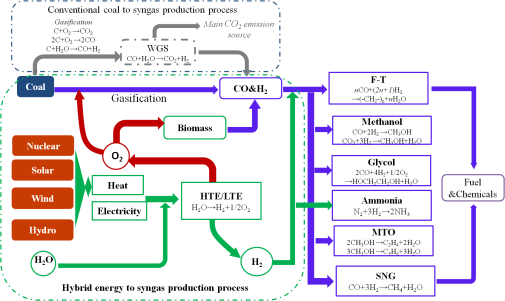
Hybrid Energy System Proposed for a Coal-Based Chemical Industry
Recently, a joint research team proposed a hybrid energy system which integrates nuclear/ renewable energy with coal for a coal-based chemical industry. The latest result was published in the famous scientific journal Joule.